From idea to finished product: this is the ethos upon which EUROEDIL builds its success. Innovation and continuous improvement is central to business growth at this progressive manufacturing company.
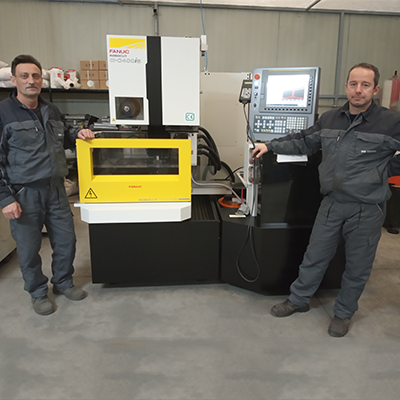
With these thoughts in mind – and faced with a growing order book and ever-shorter delivery requests from customers – EUROEDIL decided it was time for further investment in its tool workshop. In particular, the company’s production line for progressive die-stamping tools was in need of a refresh to improve output levels.
“Nearly 20 years ago in 2003 we purchased our first FANUC machine, a pre-owned wire-cut EDM manufactured in 1981,” explains Toni Dimitrievski, manager of the tool workshop at EUROEDIL Holding. “It provided trouble-free operations throughout its time on site.”
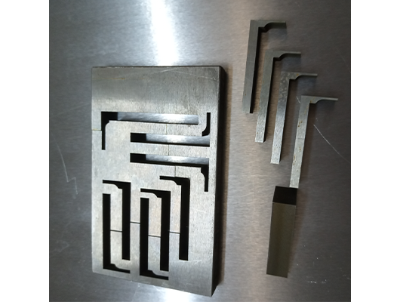
Soon bolstered by the introduction of other FANUC models, these machines provided many years of efficient and effective production at EUROEDIL. However, with the years ticking away, the company thought it prudent to invest in new machines, a move that would also provide a much-needed boost to productivity in line with its expanding order book.
“With a recent increase in work volumes and our planned company expansion, there was a clear need to invest in new machine tools,” confirms Mr Dimitrievski. “Based on our positive experience with FANUC machines we decided on a new investment: a FANUC ROBOCUT α-C400iB wire EDM and a FANUC ROBODRILL α-D14LiB vertical machining centre. Since installation and commissioning we have maximised our throughput using the new FANUC machines, largely by increasing cutting rates. Today we can manufacture die-cutting tools a lot faster and with far higher precision.”
Another significant benefit to EUROEDIL is the renowned low cost of ownership provided by all FANUC machines.
“Our older FANUC models have proved to be cost-effective as they are quite robust and rarely need repair, keeping maintenance costs low,” explains Mr Dimitrievski. “With our new FANUC machines, I can say that in the two years since installation we have not incurred any expenses for maintenance.”
He adds that the FANUC models stand out from other machines in the tool workshop, offering easier operation and maintenance supported by FANUC’s local response for service and spare parts, if required.
“Thanks to our modernisation and the installation of our two new FANUC machines we have improved our production process for die-cutting tools considerably,” concludes Mr Dimitrievski.